Robotic Process Automation to Accelerate Navy's Supply Chain
Our client partnered with CSA to assist with material control by tracking in-transit shipments from vendors and distribution centers to customers across the world.
In total, our client is responsible for the delivery of nearly $1 billion in inventory each year.
Significant time is spent managing asset shipment proof of delivery, a highly routine and labor-intensive process.
The process before RPA
Vendors post proof of shipment into an online government-owned database to notify our client of a shipment. Every other week, an Excel report with thousands of proof of shipment requisitions is compiled and shared.
Each requisition needs to be researched for proof of delivery; our client handles approximately 5,600 each month. To check proof of delivery, an inventory coordinator manually copies the document number from the Excel report and pastes it into the Navy’s asset management tracking system (ERMS – eRetrograde Management System). The coordinator then locates the full tracking number and copy/pastes it into the commercial carrier’s tracking website to get a delivery status update.
If the item was delivered, the user returns to the asset management system and submits a form prompting the recipient to update Navy Enterprise Resource Planning (ERP) and close out the record. Shipment status is also noted in the Excel file, undelivered shipment status prompt further research.
Ten inventory coordinators will process on average 67,200 documents per year. Approximately 60 percent of these requisitions require simple, repetitive processing and take about two minutes each to complete.
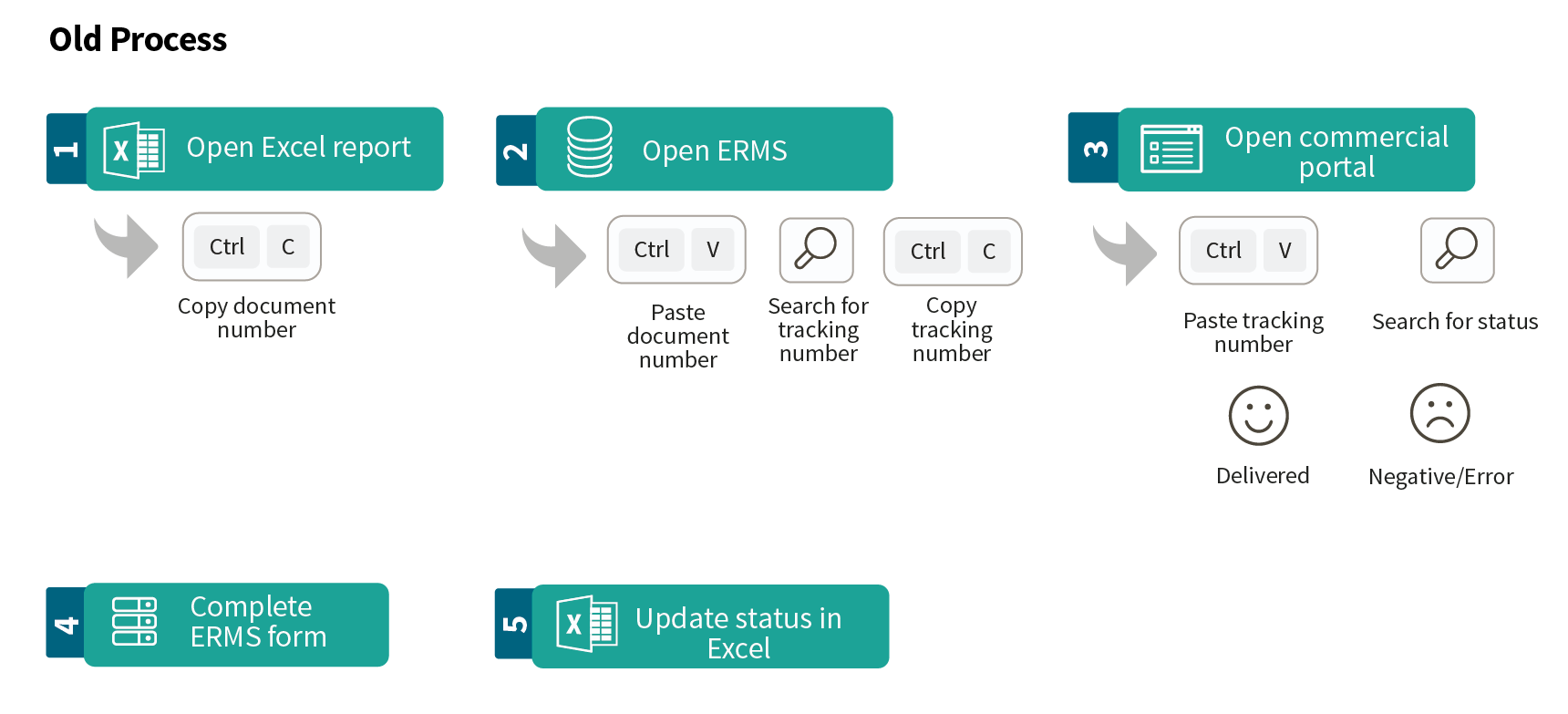
Innovate along the way
The 60 percent of shipments (40,320) that were repetitive, manual and stable required about 1,344 “people hours.” Of the ten inventory control operators, about five FTEs performed these tasks. These operations were perfect for robotic process automation (RPA).
CSA designed and implemented a robot, or a bot, to automate these mundane and time-consuming processes. Now, rather than copy-pasting document and shipping records between Excel and two websites, the inventory coordinator only runs the bot.
When prompted, the bot navigates to webpages, searches documents in the Navy asset tracking system and scrapes tracking numbers to search in the shipper’s website. If the bot finds proof of delivery on the shipper’s website, it updates the asset record in the Navy system, also updating the spreadsheet according to the outcome of each document it researches. If a document requires further research the bot marks it for manual review.
The solution was created using UiPath, increasing security and reducing vulnerabilities. The bot is configured to follow regulatory and compliance rules, which provides a document trail for auditing.
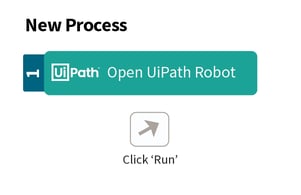
The new everyday
Inventory coordinators now utilize the bot to complete this routine, repetitive task, reducing the time spent on each requisition from two minutes to six seconds. Through these efficiency gains, we saw an initial $350,000 or 40 percent reduction of the workload, achieved by eliminating the necessity to backfill FTEs resulting from natural contract attrition. Now, only one FTE is required to accomplish the workload, saving 1,344 hours, or 70% of one person’s yearly workload. As a result, the existing employees can absorb new work requirements without additional hires. Due to the 70 percent workload reduction, there is a potential cost savings of more than $127,000 per year.
Now, tracking in-transit status takes less time and manpower and has decreased repetitive tasks providing new opportunities for our client to focus on strategic initiatives and innovation. The decreased time and errors generated by the bot allows us to ensure our client’s supervision of $960 million of inventory is managed and tracked.